Shiny Cylinders
Royce Components interviewed
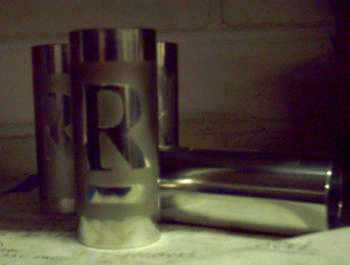
The golden era of British engineering extended, roughly speaking, from the late 19th century to the middle of the 20th. Since then, manufacturing has been in steady decline. Capital is moving the factories overseas in search of cheap labour, and our engineering expertise is following them.
But you do find occasional holdouts. The cycle industry has more than its fair share. The smart designers and engineers tend to find their way into frame prototyping or esoteric disciplines like suspension design and carbon fabrication. Unusually, Royce make components. Although there are a few trick bits in the range--carbon shells, titanium chainring bolts--the company's reputation rests on a handful of tried-and-tested hub and BB designs.
Royce HQ is in New Milton, on the Hampshire coast. Home is a 2500 foot workshop full to the rafters with high-end metalworking gear. Perching a mug of tea on a lathe stand, I met the gang: Peter Burch, Jo Moss, Kevin Charlton, and Royce's leading light, Cliff Polton. Between them, these four handle every aspect of the company's operations.
63xc.com: Cliff, your background is presumably in light engineering?
CP: Since I left school.
63xc.com: What sort of work were you doing originally? Was it automotive stuff?
CP: It was motor industry inspection jigs and fixtures when I was in London, but that changed when I moved down here in '69. It was all aircraft-based down here. My claim to fame has really got to be making the flushing toilet handles on Concorde!
63xc.com: Cycling wasn't exactly at a peak in late 70s Britain. What made you specialise in bike components?
CP: It was being asked to manufacture the first prototypes for Royce in 1979. I was a toolmaker at the time. I didn't do the design work.
63xc.com: The prototypes you showed me upstairs have a very Campag feel.
CP: They do. They were influenced by Campagnolo.
63xc.com: So how come you ended up doing work on someone else's product?
CP: I was naive. I saw the product, not the person behind it. The chap who had the company had a lot of good ideas, but he couldn't sit down and say 'right, that's the design, let's sell it.' He'd want to modify it to Mark XXV. After six months I was seriously out of pocket, so I leased the machinery back to the guy and dropped out.
63xc.com: How did you end up taking over the business?
CP: Some of the crank arms that were produced after I left turned out faulty, and that led to a big court case between Royce and their subcontractor. The bank didn't want to liquidate while all that was going on. That was a good decision, as they finished up with all the winnings. When the dust settled, I stepped in and bought up the company's assets. That was '86, '87. We started properly in '88. 63xc.com: So, when you relaunched, what components did you offer?
CP: Hubs. And bottom brackets.
63xc.com: Which is still roughly what you're doing today.
CP: That's right.
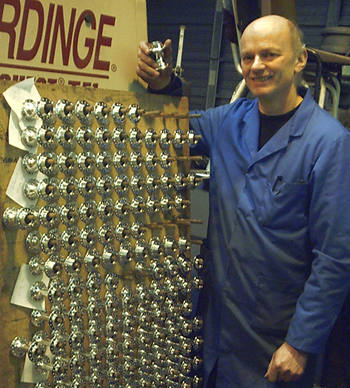
63xc.com: Which designs have you produced throughout that 20 year period?
CP: The hubs. And the bottom brackets.
63xc.com: (Laughs) What gives your designs that kind of longevity?
CP: Attention to detail. Right from the beginning we produced four lengths of BB axle. We now make many more, so many combinations in fact that it's ridiculous. So we can easily supply any requirement that someone might have.
JM: But in order to be able to supply all those, we've got to have the parts sitting on the shelf.
CP: We like selling via shops, but we don't want them to shove out a standard unit that might give the wrong chainline in some applications. We'd rather build to order.
63xc.com: So, when you receive an order for a BB or hub, how soon do you reckon to ship it?
CP: Same day.
JM: All the bits are in stock, the shells and spindles and bearings and so on. All we have to do is pull them out, build them up and send them out.
63xc.com: Let's walk through the process of making a hub. What is the raw material that arrives here? Is it aluminium and titanium billets?
CP: No, it arrives in bar form. And we work it using CNC.
63xc.com: Can you explain what CNC is?
CP: Computerised Numerical-Controlled machining. You program the computer with the shape you want and the tools you want it to use, and it goes ahead and does it.
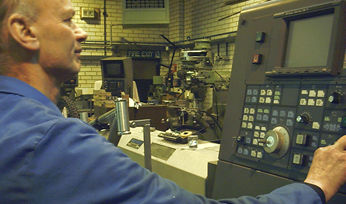
63xc.com: So it's kind of like a sculpture. You start with a block of metal, and the computer then uses various tools to cut it into shape.
CP: That's an elaborate way of putting it, but basically right.
63xc.com: I imagine that tooling up for CNC would be pretty expensive for a small shop?
CP: Yep.
63xc.com: How did you get the momentum to buy all this kit?
CP: Passion. I knew what I wanted when I took over the business.
63xc.com: Let's say that you're machining up some hub shells. What happens?
CP: You programme your design into the computer. That's probably going to take six hours. Then you run the machine. With our level of finish, it will cut about four shells an hour--but that leaves one end of the piece unmachined, the point where the machine has to grip it. So then we put it into another machine to do the other end. Then it goes to be polished, cleaned and engraved. After that is has to be drilled and countersunk, then lustred and anodised.
63xc.com: How much of that work is done here?
CP: Anodising and engraving are done out-of-house--for the volumes we do, we can't warrant doing those operations. Everything else is done by the four of us.
63xc.com: Everything?
CP: Yes. And remember, that's just the shell. We haven't talked about the other components yet.
63xc.com: Well, let's do that. Bearings for a start.
CP: We use NTN bearings.
63xc.com: Were those developed for bicycle use?
CP: Good God no! They were made for high-speed machine tool applications. They're built to superior tolerances.
63xc.com: These are sealed bearings, presumably...
CP: Yes, they have neoprene seals, contact or non-contact. Contact offers better protection, non-contact offers less friction.
63xc.com: So you use contact seals in offroad and non-contact in road applications?
CP: No, no. All our bottom brackets have contact seals, because friction is relatively unimportant in BB applications. On a hub you have two seals to worry about: one inside and one outside the bearing. For track hubs, they're both non-contact. For road and offroad hubs, we use a non-contact seal on the inside and a contact seal on the outside. But those are just the standard setups: we build whatever the customer asks for.
63xc.com: When did you start doing your offroad hubs, the Bombproof and so on?
CP: We've always done them. The Bombproof is actually our standard hub design, the one I originally came up with in 1988. But it has been updated a little bit over the years.
The original had a bronze shield over the bearings to keep stuff out. It worked OK most of the time, but if you went through deep water, the water would get in--and then it would be sealed in, it wouldn't be able to escape.
So now I work on the opposite principle: you allow water to get in behind the shield, but make sure it can get out again. There's a ten thou taper on the face behind the shield. The contact point for the seal is right in the middle, where you've got the smallest gap anyway, and the rotation of the hub will throw out mud and water before it can get that far. The only way you'll get water in there is by pressure cleaning.
63xc.com: So if I was coming back from a muddy ride, I could take a garden hosepipe and flush the mud off no problem?
CP: As long as you don't put your finger over the end of the hose. If you put your finger over the end, you're creating a higher pressure, and you'll get water syphon into the bearings.
63xc.com: I'm sure a few users have done just that?
CP: I'm saying nothing. But there's too many pressure cleaners around!
63xc.com: What about the spindles?
CP: They're one piece titanium, and they're barrel-shaped, bigger in the middle. That makes them very stiff but not too heavy.
63xc.com: What are the dimensions?
CP: I try not to quote off the top of my head--but at the outside it's 10mm, just past the dropout it's 12mm, and in the middle it's 15mm.
63xc.com: OK, that's the hubs. What about the bottom brackets?
CP: Well, we like good chainline. We make 27 different lengths of axle, and several different taper patterns. If we supplied you, say, a 115mm axle for an old Campag and you found it was too long, we'd go back to the stockroom and bring out a 112 or a 109.
63xc.com: I know of systems where you can adjust the axle position to dial in the chainline. What do you reckon to that solution?
CP: The principle is wrong. The weakest point of your axle is the area between the back of the crank arm and the bearing. If you move the axle in to get the chainline right, the crank on the non-drive side is going to be too far out.
63xc.com: What you're describing here is leverage: the force of the rider's stroke trying to bend the BB axle around the fulcrum presented by the bearing...
CP: That's right. The further the crank is from the bearing, the greater the flex and the worse the stresses. So what we do is, we try to get the bearings as far out as possible, right next to the cranks in fact, and keep them there. The axle and spacers are machined so that it's impossible to knock the bearings out of alignment by, for instance, over-tightening a cup.
63xc.com: Ti presumably allows you to have very big axles that don't weigh too much?
CP: They're barrel-shaped again. Campag's early ti axles were cut away in the centre portion like their steel ones, and that was the cause of the problems. Ours are fat in the middle to ensure rigidity. (Hands over example.)
63xc.com: Feels like about half the weight of steel.
CP: Correct.
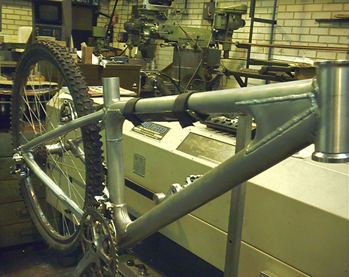
63xc.com: What else is in the pipeline?
CP: Well, I've got a frame on the go. This is the first one, the second one's upstairs, and there's five on order.
63xc.com: It reminds me of BMX geometry. Very flat, very low...
CP: It is very flat.
63xc.com: The gussets look extremely serious.
CP: The chap who built these is a coppersmith by trade. He's 70 years old, and I've never met a better sheet metal worker. Anywhere. He hammers these out by hand.
63xc.com: What's the planned use?
CP: Cross country.
63xc.com: What's the name?
CP: It doesn't have a name. The production model was going to be called the Endura, but this is the racelight version. It's lighter and it will need some special components. I'm designing a front mech, as we can't find one that works well on these large diameter tubes... These are the headtubes.
63xc.com: Very light.
CP: If anyone welds these in upside down, I shall scream.
63xc.com: I'd like to talk about Team Royce.
CP: Our relationship with them is very simple. If they want to have fun, ride responsibly, help others, then they can ride under the name of Royce. I'm not bothered how they do. As long as they get out there and enjoy themselves.
63xc.com: Who's on the team?
CP: There's a guy called Jam Price who's been with us for 15 years, and two friends from Warwick he rides with. Locally there's another group of five, including Tony Green who joined recently. He's a great rider, also enjoys cyclocross.
63xc.com: Do you find that building components for a team gives you good feedback?
CP: Feedback is always very useful and I do ride a lot myself, so I can test and discuss new ideas.
63xc.com: Tell me about Royce's involvement with Chris Boardman and the world record.
CP: Well, that started when Mike Burrows asked us to make up a BB axle for the Lotus bike, the special aero thing Chris used. It did exactly what he wanted, and the rest is history.
63xc.com: He got the record.
CP: He got the record. Unfortunately, Lotus had restricted advertising to themselves and Mavic. We weren't allowed to publicise our involvement, and neither was anyone else.
We were all bitterly disappointed that nothing happened about the Lotus. All that publicity, and, basically, they didn't want it.
63xc.com: But I believe you did some more work for Chris...
After Lotus, when Chris did his last pro race, the athlete's hour record, he asked us to provide the hubs. I knew the race was six weeks away, and I wasn't sure if we could get the wheels exactly how he wanted them in the time--they were pure custom, quite a bit different from our standard models, with special bladed spokes and so on.
We did the work anyway and he put 10 metres on a record that had stood for 28 years, since Eddy Merckx in fact. We yelled ourselves hoarse. I lost my voice for a month.
|